Balaram Bridge |
 |
Placement of The Bearings
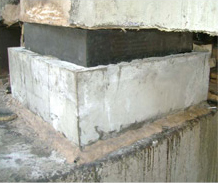 |
|
The designer was designed elastromic bearing of size 630*550*144 with 5 no. of steel laminates size of bearing. The bearing pedestals were precast 3 no. only for P3 to while P2 pedestal were in good condition but it is extended 150 mm by epoxy mortar because their was time constraints so adopted epoxy mortar.
|
The following method sequence was adopted for fixing of Bearing.
- Chipped and removed the existing plate/ rocker- roller bearing by cutting the bolts and also chipped and roughened the top portion of pier cap and bottom portion of the bearing end region of the girder.
- Provided suitable reinforcement and shuttering render the bottom portion of the girder bottom end region of the girder used epoxy mortar to get early strength & level. Similarly leveled the pier cap surface at the bearing location using epoxy mortar.
- Placed precast micro concrete bearing pedestal at bearing location and fixed all-
Round epoxy mortar and then placed new neoprene bearing pads as per design and lower the span on the new bearings.
The first lift for lifting of the superstructure started on 9th March, 2009 and the entire superstructure was lifted 60mm above the theoretical level on 12th March, 2009. The superstructure was tightly shimmed with steel plates and the jacks were kept in position with the circuit closed after transferring load to shims. Cubes of micro concrete were taken during concreting to ensure that the transfer of load to the bearings would be made only after the concrete had attained sufficient strength. The bearings were placed in proper position. The superstructure load was lifted marginally and few plates were removed after the load was transferred to hydraulic jacks. The jacks were lowered gradually till there was a gap of only 10 mm between top of the bearings.
The lowering was stopped and the actual clear gaps at all bearings were checked. As the gap of downstream was more than the gap of upstream end, the centre jack and downstream jack kept in circuit while the upstream jack rubber house valve was closed. The hydraulic circuit release valve was opened very gradually till the gap became uniform. The circuit was closed and the gap dimensions verified once again. The entire girder was scrutinized closely to ensure that the structure had not been affected in any way, the hydraulic circuit was opened gradually and the load transferred to bearings.
The top level was constantly monitored by a leveling instrument during the entire operation to ensure that the deck level attained uniform profile. The position of bearings at articulations were checked and necessary adjustment of the bearings was then carried out by placing flat jacks between the bearings and lifting one end of the articulation for resetting the bearing.
Acknowledgement
The author thank to Mr. Divakar Thakur, Construction Manager, L&T ECC,Palanpur for his active help and cooperation in this work & to Mr. Laxmikant Thakker & Tapan Thakkar of M/S Shivam concrete technology & consultancy pvt. Ltd., Varodara, who was fully associated with the rehabilitation and replacement of bearing.
|