Balaram Bridge |
 |
Work Methology Adopted
Application of polymer modified cement grout
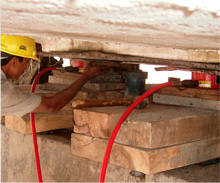 |
|
- Wearing coat was removed.
- Naked top surface was cleaned with compressor air and water jet.
- 20 mm dia holes, depth 200 mm, distance of 500 mm c/c were drilled by electrical machine and PVC nipple was fixed with polymer modified cement mortar.
- Cement=50 kg, Cebex=225 gr, water=20 lt, Tapcrete p-151=7.5 Kg. were mechanically mixed and grouting done by grout pump with compressed air pressure of 3 kg/cm2 to 5kg/cm2 and grouting was carried out till there was rejection from nipple. After grouting nipples above slabs were cut and surface was leveled with PMC mortar.
|
Application of polymer modified cement mortar
- Chipping the concrete surface up to full circumference of steel.
- Cleaning the reinforcement by wire brush then rust removal compound i.e. Reebaklens RR of Forsroc was applied then again cleaned by wire brush.
- One coat of zinc rich coating of Nitozinc Primer of Fosroc was applied.
- Bond coat- Tapcreate P-151 mixed with two part of cement by weight of thick paint & applied for bonding on new PMC.
- Cement=10 kg, sand=30 kg, Tapcreate P-151, water= 3 lt. mechanically mixed and applied in 2 layers up to 50 mm thickness
Application of epoxy mortar
- Cracks were demarcated in R.C.C. & mechanically cut in V shape groove of 20*20 mm size.
- Groove was filled with epoxy mortar 2:1:20 (Resin: hardener: Silica
sand – by weight).
Application of epoxy grouting
- Fixed 10 mm dia. metal nipple, depth 200mm, interval 300 mm in hole
in cracks and sealed hole with epoxy mortar.
- Lapox B47 & K 46 of Atul Limited in ratio of 2 resin 1 hardner by
volume is mixed and grouted with small gun attached with small air compressor at 3 Kg/ cm2 pressure from bottom to top.
- After grouting nipple above the concrete is cut and surface is leveler by PMC mortar.
Application of wrapping
- Primer- Epoxy primer Nito Wrap 30 was applied over the prepared and cleaned surface by brush and allowed to dry for 24 hours before application of saturant.
- Saturant- The mixed material of nitowrap 410 saturant was applied over the tack free primer. The wet film thickness was maintained @250 microns.
- Nitowrap glass fibre- The Nitowrap glass fibre was cut to required size and than pressed first by gloved hand on the saturant applied area then with a stiff spatula and Surface roller to remove air bubbles. One more coat of Nitowrap 410 saturant was applied over the glass fibre @ 250 microns.
Application of micro concrete
- Provided fixed water tight shuttering for pedestal.
- Mix is prepared by adding of 1part by weight of Renderoc RG Micro concrete powder of Fosroc and 1 part by weight of grit (4.75mm to10mm) and required quantity water for workability. The mixes were mixed thoroughly by mechanical stirred for about 3 mins.
- Then flowable mix were poured and there was no need for compaction as
it is flowable and self compacting mix.
|